Precision & Ergonomics
In the world of professional as well as amateur sports, the quality of the equipment can significantly impact performance. For Wilson Sporting Goods, the maker of footballs used in K-12, Collegiate, and even the NFL, precision in manufacturing is paramount. Each football is a testament to craftsmanship, requiring consistent and accurate cuts of leather panels. However, the pursuit of quality must also consider the well-being of the workforce.
Like many manufacturers, Wilson continually strives to improve output while minimizing the risk of injury to its employees. This case study examines the collaboration between Wilson and Fremont Cutting Dies to develop a lightweight, tight-tolerance die for cutting leather football panels, addressing both precision requirements and ergonomic concerns.
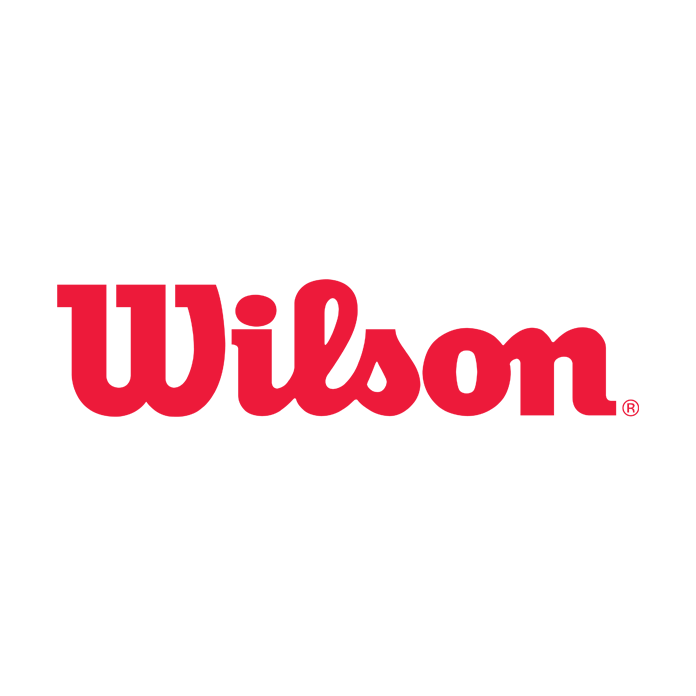
X
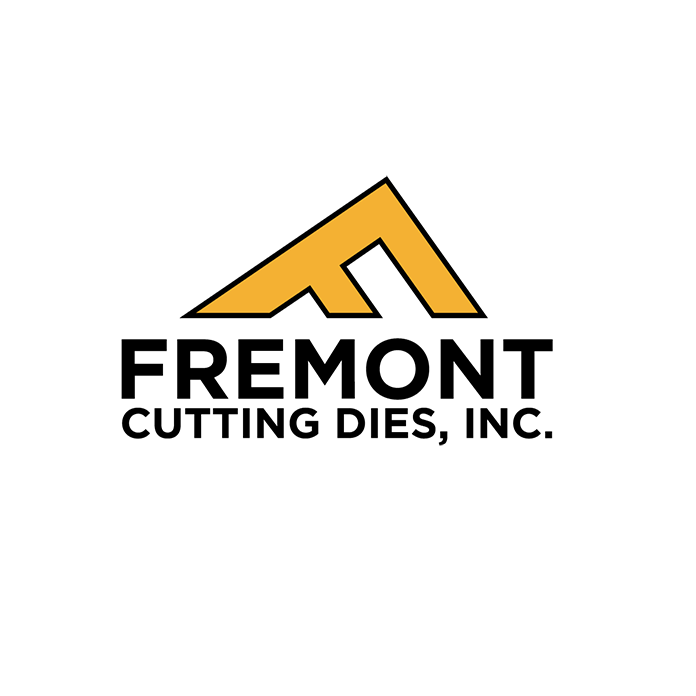
The Challenge:
Wilson’s commitment to excellence demands exacting standards for its footballs. Each leather panel must be cut with extreme accuracy to ensure consistent shape, size, and feel. Previously, Wilson used dies that, while functional, presented three key challenges.
Weight:
First, the dies weighed nearly 5 lbs, placing a significant strain on press operators who repeatedly lifted and manipulated them throughout their shifts. This repetitive motion posed a risk of musculoskeletal injuries.
Tolerance:
Second, while the existing dies produced acceptable cuts, Wilson sought tight tolerances (+/- .005″) to further enhance the quality and consistency of their footballs and to enable the automation of their cutting process. This level of precision was difficult to achieve consistently with the existing tooling.
Material:
The inherent challenges of working with leather, a material with varying thickness, texture, and flexibility, further complicated the task.
The Solution: Design & Development
Wilson partnered with us to address these challenges. The design process was a collaborative effort, with close communication and feedback loops between the two companies. Our expertise in die creation, combined with Wilson’s deep understanding of their manufacturing process, led to an innovative solution.
The resulting die was a testament to precision engineering. We employed several key design innovations. First, we selected lightweight die materials, including specialized alloys, which significantly contributed to the weight reduction. The “short and stout” design of the die structure further enhanced both lightness and rigidity, ensuring stability and accuracy during the cutting process. Critically, all features of the die were meticulously machined. This precision machining was essential to achieving and maintaining the tight +/- .005″ tolerance required for both enhanced quality and future automation. The cutting edge geometry was optimized, and precision grinding techniques were employed to ensure clean, accurate cuts.
Our development process involved multiple prototypes. Each prototype was rigorously tested to validate its performance. Testing methods included dimensional accuracy checks, cut quality assessments, and durability trials. The prototypes were put through their paces, cutting various types of leather used by Wilson. The results of these tests were carefully analyzed, and design iterations were made to refine the die’s performance and ensure it met the stringent requirements. Our team verified the consistent achievement of the +/- .005″ tolerance during these tests.
Results & Benefits
The new lightweight, tight tolerance forged die delivered significant benefits to Wilson Sporting Goods. The die weight was reduced from nearly 5 lbs to just under 3 lbs, a substantial improvement that significantly reduced the physical strain on press operators. This directly addressed Wilson’s ergonomic concerns and immediately improved the work environment.
The precision machining of the die resulted in consistently accurate cuts, achieving the target +/- .005″ tolerance. This improvement in cutting accuracy led to reduced material waste and increased production efficiency. The tighter tolerances also contributed to enhanced quality and consistency in the finished footballs.
Beyond the quantifiable results, the new die offered qualitative benefits. The lighter weight improved operator ergonomics, reducing the risk of fatigue and potential injury. The consistent and accurate cuts improved the overall quality of the footballs, potentially leading to increased customer satisfaction. Perhaps most importantly, the achievement of the tight +/- .005″ tolerance now opens the door for automation of the leather cutting process, further boosting efficiency and consistency.
Looking for Exceptional Results?
Wilson x FCD Gallery
Featured: In-Production Wilson Football Cutting Die (Photos 1-3), Wilson NCAA Football.
The Power of Collaboration
This case study demonstrates the power of collaboration and innovation in manufacturing. By working closely with Wilson Sporting Goods, we were able to develop a solution that addressed both precision requirements and ergonomic concerns. The lightweight, tight tolerance die has delivered measurable benefits, including reduced operator strain, improved cutting accuracy, increased production efficiency, and enhanced football quality.
The project also highlights the importance of considering the human element in manufacturing and the positive impact that thoughtful design can have on your worker’s well-being. The ability to achieve and maintain the +/- .005″ tolerance now enables Wilson to move forward with automating their leather cutting process, ensuring even greater consistency and efficiency in the future.
We hope our commitment to precision and practical manufacturing solutions makes us a valuable partner in your future. Do you have a problem you would like to solve? Our team is up for the challenge.