Die manufacturing plays a critical role in today’s industrial landscape. Enabling the production of countless goods you and I rely on every single day. From automotive parts to packing materials, manufacturers use dies to shape, cut, and form materials with precision and efficiency.
In this article we explore the world of die manufacturing. Including common types of dies, real-world applications, choosing quality dies, and more. By the end, you’ll be ready to take your production process to the next level.
What is Die Manufacturing?
Die manufacturing is the process of designing, engineering, and producing specialized tools known as cutting dies. Die makers utilize raw materials including tool steel, carbon steel, stainless steel, plastics, fibrous, and other man-made materials. Allowing the resulting cutting die to withstand repetitive use. The process requires advanced engineering skills and high-tech machinery to ensure accuracy and consistency.
Types of Dies in Manufacturing
Cutting Dies come in many different forms, each designed for a specific purpose in the manufacturing process. Understanding types of cutting dies is essential for selecting the right cutting die for your application. The type of cutting die affects the press required as well as how the substrate cuts, which can greatly impact the production process. Below are some of the most common types of cutting dies used across various industries.
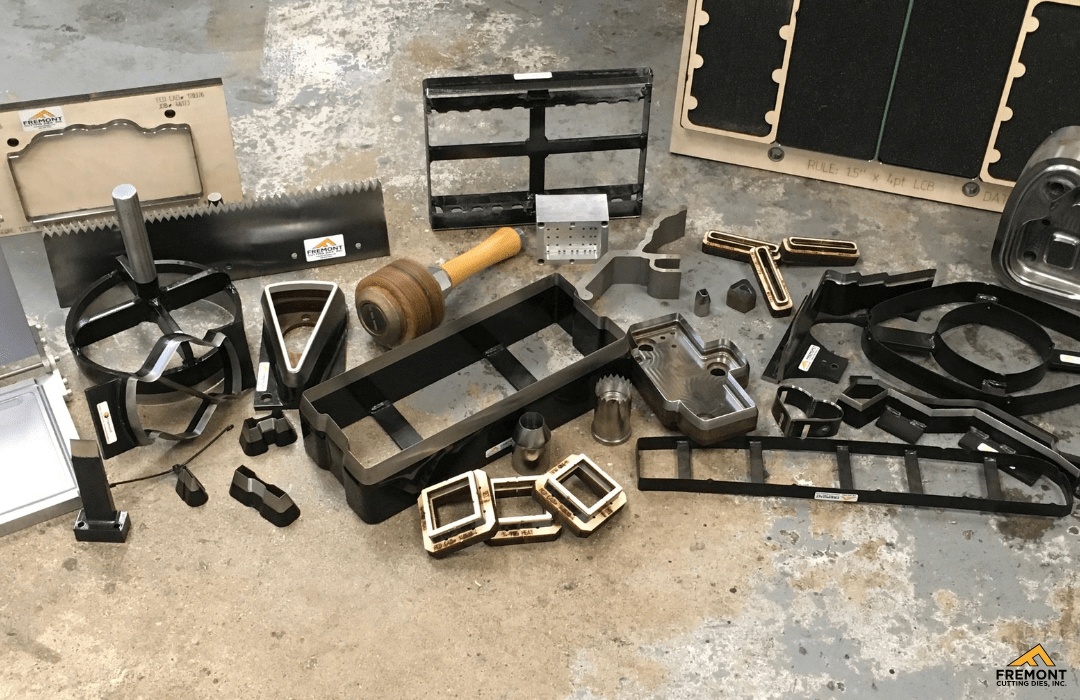
Steel Rule Dies
Steel rule dies are used to cut many types of materials into specific shapes and sizes. Steel rule cutting dies are better at cutting softer materials like paper, leather, and plastics.
Forged Dies
Forged dies are used to create strong, durable components by shaping heated metals under pressure. These dies are essential in producing heavy-duty automotive and industrial parts. Forged Dies may cut on a single plane, multiple planes or even contoured.
Specimen Dies
Specimen dies are specialized tools used for laboratory testing and prototyping. They produce precise test samples for product development and quality assurance.
Matched Metal Dies
Matched metal dies consist of two components that come together to cut materials with extreme accuracy. High-precision industries like aerospace and medical device manufacturing often utilize them.
Compound Dies
Compound dies are usually a combination of other cutting dies that can perform multiple tasks in a single stroke. One example would be combining forged die and matched metal die. The forged die could cut the perimeter shape, while the match metal could cut the detailed interior shapes.
Custom Dies
Custom dies are designed and engineered to meet unique customer requirements. These dies allow manufacturers to produce highly specialized products that standard dies cannot create.
The Manufacturing Process Overview
Step 01: Design & Engineering
When creating a cutting die, the process starts with creating detailed blueprints and CAD models. Our designers may go through several iterations of the design to ensure it will function as expected during production.
Step 02: Production
CNC machines, lathes, laser cutters and other tools along with the hands of an expert die maker craft the die components. Each type of die has a specific production process to ensure the final product will withstand rigorous production.
Step 03: Final Testing
Once production is complete, our team verifies each die meets the tolerances and requirements required. This ensures dies meet ASTM and other standards.
Step 04: Production Use
Once verification is complete, we pack up your die and ship it directly to you. Upon its arrival, a quick install into your machine and your die is ready for mass production.
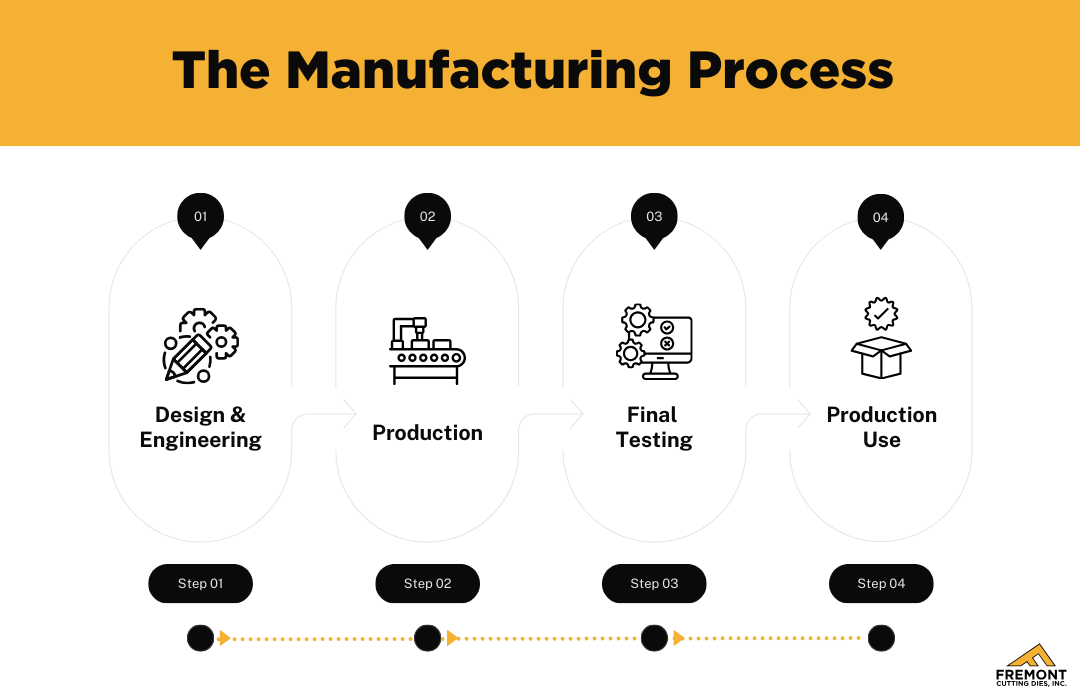
What Makes a Quality Die?
Creating a high-quality die involves attention to several key factors that ensure durability, accuracy, and performance:
Precision Engineering
Tight tolerances and precise measurements are critical for ensuring every product produced meets exact specifications.
Material Selection
The choice of materials like hardened steel or carbide ensures that dies can handle long production runs without wearing down.
Customization & Innovation
Tailoring dies to specific manufacturing needs can reduce waste, improve production speed, and enhance product quality.
Quality Control
Before shipping, the team should check the dies to ensure they meet the project requirements. For example, specimen dies meet strict tolerances to qualify for valid testing.
Key Advantages of Die Manufacturing
The die manufacturing process offers several crucial benefits that make it necessary for modern industries. Here’s a look at our top 4 benefits of using a die in your manufacturing process.
Scalable
Dies allow your business to scale production quickly and cost-effectively, making it easier to meet growing consumer demands. One die allows you to produce a large quantity of parts. While ordering multiple identical dies can boost production even further.
Consistency & Accuracy
A quality cutting die will ensure every product you produce is identical, meeting strict quality and safety standards. Even if you use two different dies to produce the same part, the result will remain uniform and consistent.
Cost-Effective
While creating custom dies requires an initial investment, the long-term savings from efficient mass production are significant. You can also experience cost savings by purchasing the proper style of die meant for your type of production runs.
Enhanced Product Quality
High-quality dies lead to high-quality products, boosting customer satisfaction and reducing production errors. Both factors will create a more cost-effective and sustainable product in the long run.
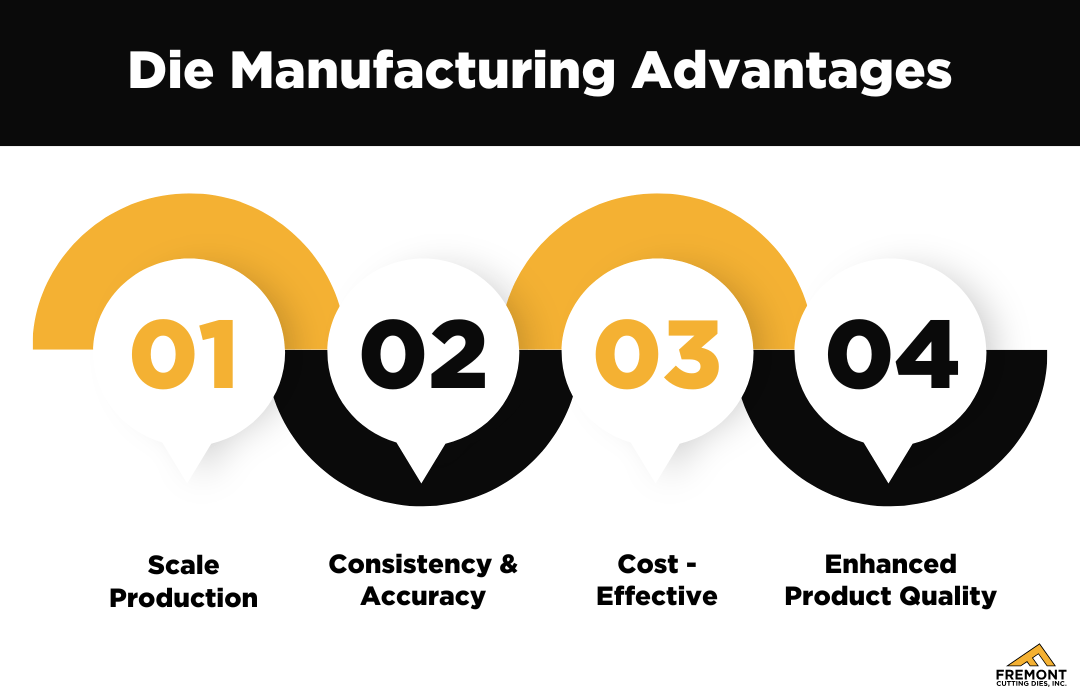
Popular Industries that Utilize Dies
Dies are integral to modern manufacturing processes, enabling the mass production of components with consistent quality, precision, and efficiency. Dies allow the production of complex parts with minimal waste. Here are a few common industries and how they utilize dies.
Automotive Industry
Dies create everything from interior car body panels and battery insulators to transmission gaskets. The automotive sector depends on cutting and forming dies to produce safe and reliable vehicles that meet strict standards.
Packaging Industry
Packaging products like boxes, labels, and custom containers are made using cutting and forming dies. These dies allow manufacturers to produce products quickly. Ultimately keeping per piece cost low to match consumer expectations.
Consumer Goods
The list of consumer products that require a die in their manufacturing has no end. Everything from your shoes to cell phones and tools to home appliances rely on dies for shaping and cutting components.
Why Choose a Professional Die Manufacturer?
Partnering with an experienced die manufacturer can significantly impact the success of your production process:
Expertise & Experience
Skilled die makers understand complex industry requirements and can offer valuable design insights.
Customization & Support
Professional die manufacturers can create custom solutions tailored to unique product specifications.
Long-Term Reliability
A well-made die from a reputable manufacturer ensures long-lasting performance and lower maintenance costs.
Key Takeaways
You can see by now that die manufacturing is the backbone of modern production. Enabling the creation of countless products with precision, efficiency, and reliability. Regardless of your industry, a high-quality cutting die will ensure your production processes run smoothly and cost-effectively. When thinking about purchasing new dies or retooling existing ones, it’s important to choose the right die manufacturer.
Are you looking for a trusted die manufacturer? Contact us today to learn how we can help with your production needs. We create precision-engineered dies built to last.